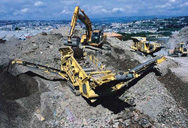
How can I determine the best RPM and balls to powder ratio for wet Ball ...
2023年3月14日 I want to ball mill 60 gm of Al powder in steel jar with 10mm diameter ball size. What will be the quantity of balls to be taken for ball milling?
Consulter un spécialiste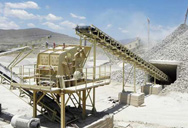
Critical rotation speed for ball-milling - ScienceDirect
1999年8月3日 Critical rotation speed of dry ball-mill was studied by experiments and by numerical simulation using Discrete Element Method (DEM). The results carried out by both
Consulter un spécialiste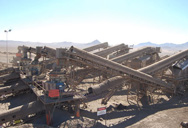
(PDF) Optimization of the ball mill processing
2016年1月1日 The aim of this study was to determine the effect of main milling variables, i.e. agitator shaft speed (50%, 75%, and 100%, which is 25 rpm, 37.5 rpm, and 50 rpm) and milling time (30, 45,...
Consulter un spécialiste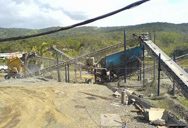
A study on a new algorithm to optimize ball mill system
2010年4月1日 In this paper, we preliminarily focus on the optimization operation for ball mill pulverizing system in power plant. The non-linear model of electric consumption is built based
Consulter un spécialiste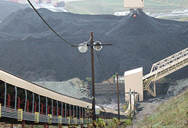
Ball milling process variables optimization for high-entropy
2023年9月1日 The most optimal processing condition can be predicted from the main effect plot for S/N ratio. The optimal factors levels that minimize the grain size or maximize S/N ratio are
Consulter un spécialiste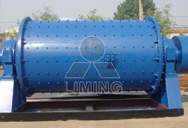
Navigating Ball Mill Specifications for Theory‐to‐Practice ...
2024年8月15日 Commonly reported parameters such as time, rpm, and ball mass are often insufficient to replicate mechanochemical syntheses accurately. By demonstrating that
Consulter un spécialiste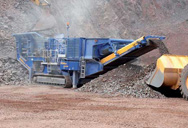
Effect of ball size and powder loading on the milling
optimal ball size at which the most reduced average particle size is achieved among other investigated ball sizes. The ball diameter of 5 mm is optimal at 50 rpm of rotation speed (the
Consulter un spécialiste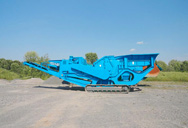
Comparative Study on Improving the Ball Mill Process
2021年2月19日 The optimum process parameters setting concluded that balls to powder weight ratio are 20:1, the optimum ball mill working capacity is 2 L while the optimum speed of the ball
Consulter un spécialiste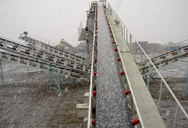
Ball Mill Operating Speed - MSubbu Academy
2024年4月30日 The critical speed of ball mill is given by, \(\displaystyle n_c = \frac{1}{2\pi}\sqrt{\frac{g}{R-r}} \) where R = radius of ball mill; r = radius of ball. For R = 1000
Consulter un spécialiste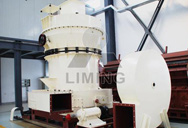
A new planetary ball mill device with adjustable speed ratio
When impact energy and milling power is plotted against the different speed ratios, this relationship is clear to observe, that at the point of optimal impact energy there is a dip in the milling power.Such nonlinear behavior makes the PBM performance difficult to predict. There is also the fact that this idealized model does not take the influence of ball-to-ball indirect impact
Consulter un spécialiste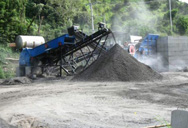
How to Improve Ball Mill Performance - 911Metallurgist
2017年10月25日 Ball mill circuit classification system performance is considered here first because it provides the basis for subsequent characterization of ball mill breakage efficiency. Major design and operating variables in closed circuit ball milling of a specified feed to a desired product size are summarized in Table 1.
Consulter un spécialiste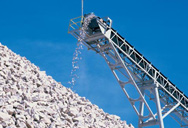
(PDF) Effects of Ball Size Distribution and Mill Speed and
2020年7月2日 A grinding circuit simulation combined with ball weal law was used to determine the optimum composition of the make-up ball sizes in tumbling ball mills. It was found that the optimum composition ...
Consulter un spécialiste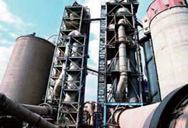
Critical rotation speed for ball-milling - ScienceDirect
1999年8月3日 Critical rotation speed of dry ball-mill was studied by experiments and by numerical simulation using Discrete Element Method (DEM). The results carried out by both methods showed good agreement. It has been commonly accepted that the critical rotation speed is a function of a ball radius and a jar diameter. The results of the present work ...
Consulter un spécialiste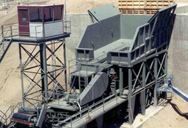
THE REVOLUTION IN ULTRAFINE GRINDING - RETSCH
Controlled forces provide optimum results in a short time. Emax – The Revolution in Ultrafine Grinding The Emax is an entirely new ball mill designed for high energy grinding. The maximum speed of 2000 rpm, so far unrivaled in a ball mill, and the innovative jar design produce highly effective size reduction by impact and friction. The grinding
Consulter un spécialiste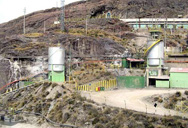
Comparative Study on Improving the Ball Mill Process
2021年2月19日 The optimum process parameters setting concluded that balls to powder weight ratio are 20:1, the optimum ball mill working capacity is 2 L while the optimum speed of the ball mill is 105 rpm. Using SEM characterization, the improved particles of silica sand presented a spherical shape with a cluster.
Consulter un spécialiste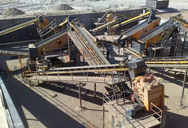
Effect of ball size and powder loading on the milling
optimal ball size at which the most reduced average particle size is achieved among other investigated ball sizes. The ball diameter of 5 mm is optimal at 50 rpm of rotation speed (the resultant average particle size of the milled powder is 2.3 μm), ball diameter of 3 mm is optimal at 100 rpm (1.4 μm), and Fig. 1. Percent passing of milled Al 2O
Consulter un spécialiste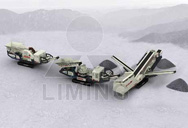
ball mill rpm - planetary ball milllaboratory ball milllab
2024年10月7日 When the mill operates at a low RPM, the balls primarily roll over the material, leading to a slow rate of particle size reduction. In contrast, when the RPM increases, the balls achieve a higher velocity, allowing them to be lifted to a greater height before falling onto the material. This impact results in more efficient particle size reduction.
Consulter un spécialiste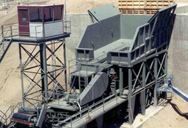
ball mill rpm - planetary ball milllaboratory ball milllab
2024年10月7日 However, there exists an optimal RPM range that varies depending on the mill’s diameter, the material being processed, and the desired final particle size. Exceeding the optimal RPM can lead to a phenomenon known as centrifugal force, where the balls are thrown away from the grinding zone, thus reducing the effectiveness of the grinding process.
Consulter un spécialiste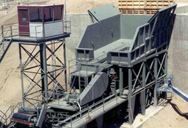
ball mill rpm - planetary ball milllaboratory ball milllab
2024年10月7日 However, there exists an optimal RPM range that varies depending on the mill’s diameter, the material being processed, and the desired final particle size. Exceeding the optimal RPM can lead to a phenomenon known as centrifugal force, where the balls are thrown away from the grinding zone, thus reducing the effectiveness of the grinding process.
Consulter un spécialiste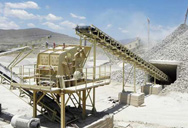
ball mill critical speed calculation – stone cruxder
Welcome to our blog post about ball mill critical speed calculation! If you’re curious about the fascinating world of ball mills and want to understand their importance, then this article is for you. Whether you’re a seasoned engineer or just starting out in the field, understanding the critical speed of a ball mill is essential knowledge.
Consulter un spécialiste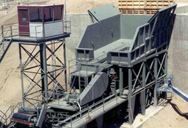
ball mill rpm - planetary ball milllaboratory ball milllab
2024年10月7日 However, there exists an optimal RPM range that varies depending on the mill’s diameter, the material being processed, and the desired final particle size. Exceeding the optimal RPM can lead to a phenomenon known as centrifugal force, where the balls are thrown away from the grinding zone, thus reducing the effectiveness of the grinding process.
Consulter un spécialiste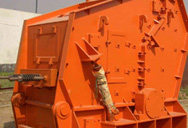
Mastering Tapered Ball Nose End Mill: Optimal Feeds and
2023年6月15日 Understanding the Unique Design of Tapered Ball Nose End Mills. Tapered ball nose end mills are characterized by their distinctive geometry, which features a gradually decreasing diameter along the cutting length, culminating in a hemispherical tip. This unique design offers several advantages over traditional end mills:
Consulter un spécialiste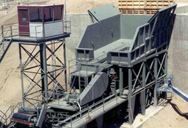
ball mill rpm - planetary ball milllaboratory ball milllab
2024年10月7日 However, there exists an optimal RPM range that varies depending on the mill’s diameter, the material being processed, and the desired final particle size. Exceeding the optimal RPM can lead to a phenomenon known as centrifugal force, where the balls are thrown away from the grinding zone, thus reducing the effectiveness of the grinding process.
Consulter un spécialiste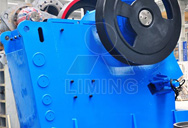
(PDF) Kajian Produksi Ball Mill Dalam Menentukan Efektivitas ...
2020年10月1日 In this study, the variables used are feed rate, number of Ball Mill revolutions (RPM), and water rate. The experiment was used 27 times by setting variables in combination to get effective ...
Consulter un spécialiste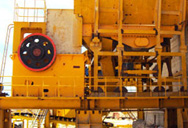
Ball mill characteristics and test conditions Mill Diameter, D
Ball mill characteristics and test conditions Mill Diameter, D (cm) 20.4 Length, L (cm) 16.6 Volume, V (cm 3 ) 5,423 Operational speed, Ν (rpm) 66 Source publication
Consulter un spécialiste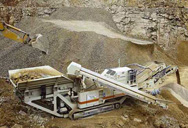
Planetary Ball Mill Process in Aspect of Milling Energy
2014年4月28日 The optimal ratio was found to be 1.15 at 800 rpm. 4. ... Electrodes made using ball mill mixing exhibited a porous structure, enabling more AM-electrolyte contact, thus improving ionic ...
Consulter un spécialiste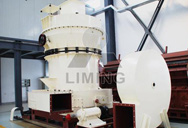
What is the optimal rotation speed for a ball mill? - LinkedIn
2023年2月13日 The ideal rotational speed of a ball mill for optimal grinding depends on several factors such as the size and weight of the grinding media, the size of the mill, and the material being processed.
Consulter un spécialiste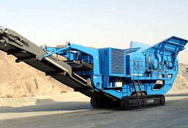
Finally got a ball mill, Tips? - Tools and Tooling - APC Forum
2021年6月14日 I use this media in my ball mill works great. 1/2-Inch Hardened Lead Ball Milling Media — Skylighter, Inc. ... and it will use around 75 of those balls. The stock mill runs at around 60 rpm. 90 rpm is ideal for that diameter jar. Easily done by cutting a section of vinyl tubing (Home Depot etc, a buck or two), splitting it with a knife, and ...
Consulter un spécialiste